Facts About Alcast Company Revealed
Table of ContentsAlcast Company for BeginnersAlcast Company - An OverviewIndicators on Alcast Company You Should KnowThe Best Strategy To Use For Alcast CompanyAlcast Company Things To Know Before You Get ThisThe Definitive Guide for Alcast Company
The refined distinction hinges on the chemical material. Chemical Contrast of Cast Light weight aluminum Alloys Silicon promotes castability by minimizing the alloy's melting temperature level and improving fluidity during spreading. It plays a crucial function in permitting detailed molds to be filled up precisely. Furthermore, silicon adds to the alloy's strength and wear resistance, making it important in applications where sturdiness is important, such as vehicle components and engine parts.It likewise improves the machinability of the alloy, making it easier to process right into completed items. In this way, iron adds to the overall workability of light weight aluminum alloys. Copper increases electric conductivity, making it helpful in electric applications. It likewise improves corrosion resistance and includes in the alloy's total stamina.
Manganese contributes to the toughness of light weight aluminum alloys and enhances workability (Aluminum Casting). It is generally made use of in wrought aluminum items like sheets, extrusions, and profiles. The visibility of manganese aids in the alloy's formability and resistance to cracking throughout fabrication procedures. Magnesium is a lightweight aspect that provides stamina and impact resistance to light weight aluminum alloys.
All About Alcast Company
Zinc boosts the castability of aluminum alloys and assists control the solidification procedure throughout casting. It improves the alloy's strength and solidity.

The key thermal conductivity, tensile toughness, yield strength, and prolongation vary. Among the above alloys, A356 has the greatest thermal conductivity, and A380 and ADC12 have the least expensive.
The 10-Minute Rule for Alcast Company
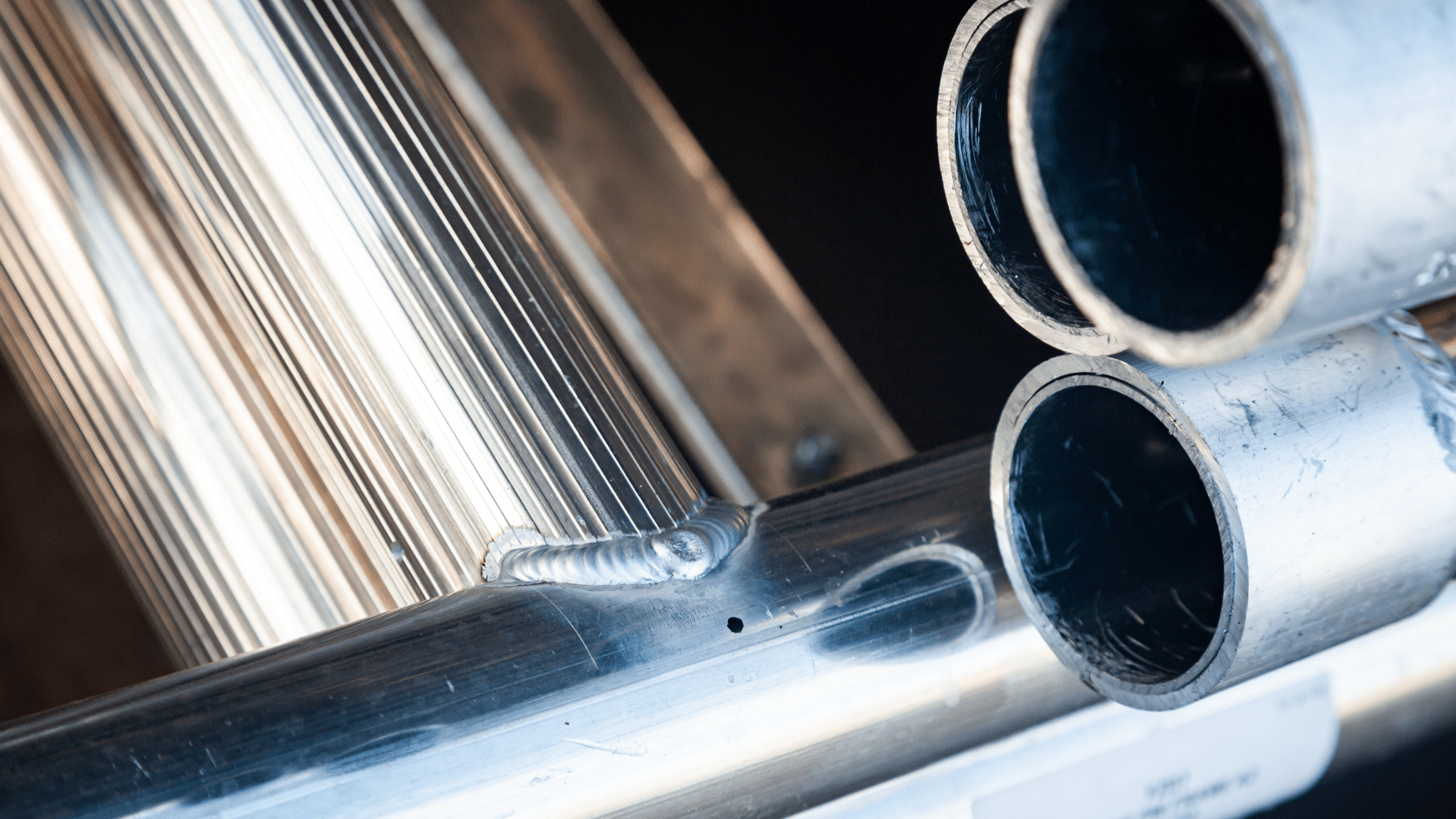
In accuracy casting, 6063 is fit for applications where elaborate geometries and high-quality surface coatings are paramount. Examples consist of telecommunication units, where the alloy's superior formability enables streamlined and cosmetically pleasing designs while preserving architectural integrity. Likewise, in the Lights Solutions industry, precision-cast 6063 elements develop stylish and effective lighting components that need complex shapes and great thermal efficiency.
It leads to a finer surface area coating and much better rust resistance in A360. Furthermore, the A360 displays remarkable prolongation, making it suitable for complex and thin-walled components. In precision spreading applications, A360 is appropriate for markets such as Consumer Electronic Devices, Telecommunication, and Power Devices. Its improved fluidity enables for complex, high-precision elements like mobile phone cases and communication device housings.
Rumored Buzz on Alcast Company
Its one-of-a-kind properties make A360 a useful choice for accuracy spreading in these markets, boosting item longevity and quality. Light weight aluminum alloy 380, or A380, is a commonly utilized casting alloy with a number of distinctive features. It provides exceptional castability, making it a perfect option for precision casting. A380 displays excellent fluidness when molten, making sure detailed and comprehensive molds are precisely reproduced.
In precision casting, aluminum 413 radiates in the Consumer Electronics and Power Devices markets. This alloy's remarkable rust resistance makes it an outstanding choice for exterior applications, making certain durable, long lasting products in the discussed sectors.
Alcast Company Fundamentals Explained
Once you have decided that the light weight aluminum die casting procedure appropriates for your project, a critical following step is picking the most ideal alloy. The aluminum alloy you select will considerably affect both the spreading procedure and the properties of the last item. Due to this, you need to make your decision carefully and take an educated technique.
Identifying the most appropriate aluminum alloy for your application will indicate considering a large variety of features. These relative alloy features comply with the North American Pass Away Spreading Organization's guidelines, and we have actually separated them right into 2 classifications. The initial group addresses alloy features that impact the production procedure. The 2nd covers attributes impacting the homes of the end product.
More About Alcast Company
The alloy you pick for die spreading directly impacts several facets of the spreading procedure, like exactly how very easy the alloy is to collaborate with and if it is prone to casting issues. Hot fracturing, additionally referred to as solidification fracturing, is a common die spreading issue for aluminum alloys that can cause internal or surface-level rips or cracks.
Particular light weight aluminum alloys are a lot more vulnerable to warm cracking than others, and your choice should consider this. One more usual defect found in the die spreading of aluminum is die soldering, which is when the cast sticks to the die wall surfaces and makes ejection hard. It can damage both the cast and the die, so you must look for alloys with high anti-soldering residential or commercial properties.
Rust resistance, which is already a remarkable attribute of aluminum, can vary considerably from alloy to alloy and is pop over here a necessary characteristic to take into consideration relying on the ecological problems your item will be exposed to (aluminum metal casting). Put on resistance is one more residential property generally looked for in aluminum items and can separate some alloys